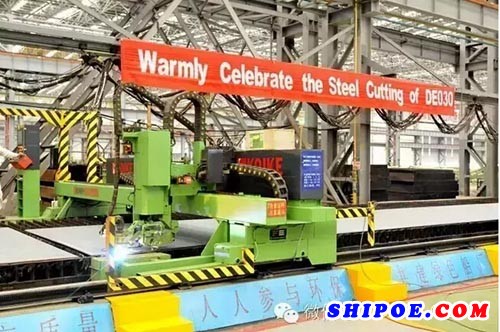
近年来,欧美等发达国家提出“再工业化”战略,强力推动“制造业回归”,以智能制造为代表的高端制造是这些国家实现“再工业化”的主要手段,新一轮工业革命正在掀起热潮。发达国家在智能制造领域采取了一系列的行动和措施,其中包括:德国“工业4.0”,美国“产业互联网”,日本“机器人新战略”等。“中国制造2025”已经上升到国家战略,是企业发展的必经之路。
作为我国第一家中外合资造船企业,南通中远川崎船舶工程有限公司紧跟国家宏观政策步伐,前瞻性地完成了散货船、集装箱船、油轮三大主流船型及汽车滚装船、多用途船等多产品的开发与升级换代,并在相关技术方面领跑中国造船、走在世界先进行列。
早在2006年,南通中远川崎船舶工程有限公司便超前谋划,着手生产、设计的信息化改造,并积极寻求突破,将扩大机器人应用和实施生产线改造等智能制造手段作为信息化和工业化深度融合的切入点,以大幅度减少人工成本、减轻劳动强度、改善作业环境、提高生产效率、降低产品不良品率,从而持续提升企业竞争力。2012年至今,南通中远川崎已先后建成4条机器人生产线,成为全国样板。今年7月,该公司智能化车间被确定为国家工业和信息化部智能制造试点示范项目,国内造船企业独此一家。
由中国远洋运输(集团)总公司与日本川崎重工业株式会社合资兴建的南通中远川崎船舶工程有限公司,主要从事中、高端船舶的研发和建造,产品类型涵盖各型散货船、大型集装箱船、超级油轮、矿砂船、汽车滚装船等主流船型,以及多用途船、双燃料船、LNG船等特种船,年生产能力约300万载重吨。公司成立以来,实现了高起点、跨越式发展,迄今共交付各种远洋船舶170余艘,其中,30万吨超级油轮、30万吨矿石运输船、13386标箱集装箱船等多个船型,填补了中国造船业多项空白。建造工时、钢材利用率、万美元产值耗电量、生产效率等主要经济技术指标达到国内领先、国际先进水平,先后被认定为“江苏省船舶技术工程研究中心”、“江苏省博士后创新实践基地”、“江苏省两化融合示范企业”,3次被认定为国家级“高新技术企业”。
2007年,南通中远川崎公司大规模利用信息技术改造传统设计建造手段,升级改造计算机集成制造系统功能,进一步提升信息系统的应用范围和信息系统集成度,扩大数字化制造装备的使用规模,实现了以信息化和工业化深度融合为标志的数字化造船。经过几年的开发、创新和实践,建立了完善的计算机集成制造系统,将贯穿船舶产品全生命周期的CAD、CAPP、CAM 、ERP等应用高度集成,在研发、设计、采购、制造、财务、管理等流程中实现信息化和数据共享,并由此获得“江苏省两化融合示范企业”称号。
2012年,南通中远川崎确立了将智能造船作为转型升级的主攻方向和实现造船强厂的主要途径,4条机器人生产线相继投产。通过不断攻关,初步建立了以数字化、模型化、自动化、可视化、集成化为特征的智能化造船和生产管理体系,真正实现了研发、设计、生产、管理等环节全面融合、协同运行,具有示范作用的船舶制造智能车间初具规模。船舶制造智能车间建设,实现了各加工系列的智能制造,达到工装自动化、工艺流水化、控制智能化、管理精益化,保障了产品质量的稳定,缩短了加工周期,极大地提高了生产效率,产品质量和建造效率达到世界先进水平。
通信网络系统覆盖全厂
作为船舶智能车间的基础设施建设,南通中远川崎建立了覆盖全厂的计算机网络系统,通过光纤连接到各生产车间,并借助计算机网络,实现物理制造空间与信息空间的无缝对接和映射,为精细化和智能化管控提供基础。
技术研发部门通过CAD、CAPP、CAM、虚拟仿真等技术的运用,来实现产品研发设计的数字化。利用生产运行数据和设计数据,将现场作业、运营、管理等固化成各类工艺、业务模型和规则,根据实际需求选择适用的模型来适应各种生产管理活动的具体需要。
同时,还利用数字专线连接大连中远川崎船舶工程有限公司,实现两家船厂异地协同,设计、采购、经营等信息共享。
1.计算机辅助设计(CAD)系统
TRIBON系统在南通中远川崎公司船、机、电等各专业领域得到广泛运用,数字化样船高度集成。包括船体构造、管系、主要机器设备等在内的所有部件,均在计算机内设计完成。通过计算机网络,可实现多专业设计人员的并行设计、协同设计、实时数据共享。同时,对计算机辅助设计系统进行了大量的二次开发,使其与设计及制造体系紧密结合,减少了大量重复作业和错误作业,有效提高了设计、制造的质量与效率。
2.计算机辅助工艺设计(CAPP)
该公司开发的CAPP系统,可提取CAD系统中所有的设计数据,并根据规范要求和生产条件进行批量的数据加工处理,从而自动生成符合制造加工要求的生产图面及数据,同时把与建造工艺相关的焊接收缩量、加工精度和余量等信息标准化或基准化,运用到船舶三维设计模型中。
3.计算机辅助加工(CAM)
利用基于DNC车间管理模式,将制造过程有关的设备(如数控切割机等)与上层控制计算机集成为一个系统,从而实现制造设备与上层计算机之间的信息交换,通过接收CAD和CAPP系统处理完的数据,并将数据传输至数控切割机和机器人设备,实现了从钢板下料开始到切割成品产出的自动处理。
智能制造系统领先一步
南通中远川崎在船舶智能化制造方面,率开国内先河。高度自动化的流水作业生产线加上柔性化的船舶生产工艺流程,实现了船舶制造的自动化操作和流水式作业。
1.型钢生产线
型钢是船体常用部材之一,原先的生产方式,从划线、写字到切割、分料,完全采用手工作业,效率低,周期长,劳动强度大,且难免出现误操作。型钢自动化生产线建成后,实现了从进料→切割→自动分拣→成材分类叠放全过程的智能制造,包括物料信息传输和物料切割智能化以及物料分类感知智能化,配员由原来的20人减少为7人,有效减少了人工成本,缩短了生产周期,降低了劳动强度,为后续扩大机器人应用积累了经验。
2.条材机器人生产线
条材是分段制造的主要部材之一,它的特点是数量多,大部分部材比较短小。原来的生产方式,包括划线、写字、开条、端部切割、打磨、分料等全是手工作业,效率低,生产周期长,容易出错。条材机器人生产线的投产,实现了信息传输和物料传输感知智能化以及加工智能化,配员由原来的22人减少为8人,提高了生产效率,缩短了生产周期,降低了劳动强度。
3.先行小组立机器人生产线
尽管造船中厚板电弧焊接实现机器人作业困难很多,但南通中远川崎还是从最简单的先行小组材开始,推进机器人焊接。传统的制造方式是,钢板在定盘上全面铺开,一块一块地装配、焊接、翻身、背烧,占用面积大,制造周期长,效率低。先行小组立机器人生产线投产后,实现了工件传输和焊接智能化,以及自动背烧、自动工件出料。整条生产线仅配一名员工操作,配员减少一半以上。
流水线生产方式是工业化大生产的必然要求。对造船业而言,车间内生产作业的流水线化将是今后实施船舶智能制造的一个重要发展方向。目前南通中远川崎已实施了大舱肋骨生产线、Y龙筋生产线、焊接装置等数个半自动化生产线技改项目,取得了良好的效果。
4.智能物流系统
公司采用“横向到边、纵向到底”的设计原则,建立了功能完善的智能物流系统,并与设计系统高度集成,从而将企业的人力、资金、信息、物料、设备、时间、方法等各方面资源充分调配和平衡,为企业加强财务管理、提高资金运营水平、减少库存、提高生产效率、降低成本等提供强有力的工具。
南通中远川崎的智能造船模式使设计、制造、加工、管理信息一体化,贯穿了零件设计信息、工艺信息、工装信息、材料配套信息、加工信息和装配信息的信息生成和传输全过程,并且在采购申请单、物料清单、托盘清单等业务方面全面实现了无纸化。据了解,该公司在未来发展中还将继续扩大工业机器人应用。