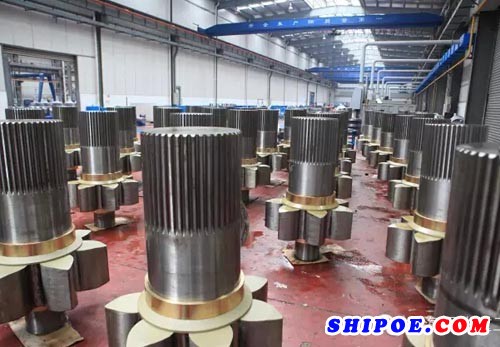
9月14日的苏通大桥上,如寻常般忙碌。穿梭来去的车辆,见证了大桥下又一艘石油钻井平台“冉冉”升起。
这艘被命名为“振海2号”的400英尺石油钻井平台,是振华重工制造的第二艘平台,在经历了全抬升测试后,即将完成全部试验。
钻井平台的配套件尤其是核心部分,从前国内平台制造厂家只能依赖进口。“海洋石油981号”总造价60亿元,其中近40亿的设备为国外进口,这其中包括升降系统、钻井包等核心装备。
与国内其他公司生产的平台不同,振华重工不仅造“壳” ,还注重造“芯” 。在多个平台配套件上迈开了国产化步伐,这其中包括平台升降系统、滑移机构和电控系统等。
升降系统主要包括升降单元、锁紧系统和桩腿,这些是自升式平台的核心部件。桩腿一方面起到支撑作用,另一方面也是平台升降时的轨道,升降单元则提供上下运动的动力,锁紧系统提供平台到达指定高度后的锁定“握力” 。
作为升降系统技术含量最高的部件,升降单元的设计和制造尤其复杂。
原型试验赢得进军世界通行证
2012年1月29日,正月初七,新年开工第一天,人们还徜徉在节日的喜气中。
美国船级社的验船师赵宏权,前一天还在海南度假,今天就“直飞”到了振华重工南通传动的试验现场。在这里,国内制造平台升降单元将首次进行美国船级社认证的原型试验。试验进行得十分顺利,让赵宏权和在场的振华重工工程师们格外开心。
陈贻平是振华重工南通传动负责现场工艺和技术的副总经理,虽然他自认为心里很有底,但等试验完全完成,机器停止了转动,他才长吁了一口气。
试验方案是经船级社认可的,试验的仪表都经过了确认,试验程序要求定时截屏,试验全程由专人录像。“虽然对设计和制造都有把握,但是这关键的大考顺利过关,才说明振华重工的平台升降单元具有了进军海洋的通行证。 ”陈贻平表示。
原型试验通过模拟恶劣工况下的长时间运转,然后分拆检测部件的可靠性,来判断产品的性能,它是海工产品走向市场的必经之路。
次日的拆检,依然没有发现任何异常。赵宏权竖起了大拇指:“你们将拿到美国船级社在中国大陆地区第一张平台升降单元的原型试验证书。”
一同在场见证的,还有来自中国交建旗下美国F&G公司的工程师阿尔弗雷德,在他近乎苛刻的全程紧盯“扫描”下,升降单元的试验和探伤检测全部过关。
2010年,中国交建以高出对手25 %的溢价收购了这家有着60多年平台设计经验公司的全部股权。完成收购几个月后,振华重工就与F&G签订了合作协议,为正在独立研制的平台升降单元带来了携手“巨人”的机遇。
此后双方合作也非常顺利,自2011年开始, F&G凭借一流的平台设计方案, 100多个海上作业平台的设计经验,给振华重工带来了专家级的指导和交流。正如当年F&G公司总裁所分析的,F&G和振华重工的“联姻” ,设计和制造的有机互补是重要原因。
强强联手,进一步激发了振华重工潜在的制造优势, F&G先后将18个自升式石油平台的升降单元订单交给了振华重工,让振华重工的海工配套产品走向了世界。
在过去的4年多时间里,振华重工为全球70 %新开工的自升式平台提供了近2000套升降单元,包括美国、新加坡、阿联酋及国内用户。振华人的不懈努力,换来了行业市场的认同。
制造升级破解批量生产难题
三年多的时间,生产2000多套升降单元。说起当初批量生产的曲折,南通传动副总经理汪南感慨万千。
南通传动作为具有多年机械制造经验的配套件生产基地,一直承担着振华重工核心配套件齿轮箱等制造和海工新产品试制任务。制造优势在国内首屈一指,然而,制造如此大量的升降单元不是轻而易举的事情。
“试制中的成功,并不能代表批量生产完全没有问题。 ”汪南说道。多年的新品试制经验,让振华人始终保持着清醒。果然,后面的发展应验了这番话。
“升降单元行星减速器部分,行星架有五个均布的孔。当时用普通镗床加工,效率很低,生产进度跟不上。 ”升降系统生产主管王宣仲还记得当时的窘迫。按照计划,当时一个月需要完成一个平台升降单元,也就是54台抬升减速箱的生产任务,平均下来每天至少得完成两台。
“其实,效率是一个方面,普通镗床的精度也无法保证。 ”项目组对加工方法进行了研究,决定采用数控镗床加工,但是现有的刀具无法满足要求,只能上专用防震刀具。为此,项目组又对现有市场上的刀具进行细致研究。
在一步步的研究下,终于一天可以加工3至4个行星架,一个瓶颈被打破。但另一个瓶颈很快又暴露了出来,这次是卡壳在抬升大齿轮爬齿花键加工上。不过有了经验,项目部驾轻就熟。
类似的加工创新还有很多,如行星架联板加工中采用成型刀具,七齿大齿轮改钻排加工为锯削加工,等等。
设计推动了制造升级,一批创新的制造工艺方案应运而生。在升降单元、锁紧系统、平台齿条桩腿零部件加工和后期装配中,为实现市场化创新的工装和工艺方案,先后获得多项实用新型专利和发明专利。张洋是南通传动的一名工艺工程师, 5月,他参与的《海洋平台抬升减速器轴承间隙调整方法》顺利获得了国家知识产权局的发明专利证书。而在此前几天,由张建国等一线工程师研发的《一种海洋工程用减速箱箱体用组合定位工装》也顺利获批为实用新型专利技术。多年的制造和装配工艺研究,让这群年轻的海工一线工程师迅速成长起来。
在大型自升式平台升降系统关键技术研发与应用项目中,振华重工已拥有7项发明专利、 17项实用新型专利、 10多篇相关专业论文。
钻石品质从暴风试验到破坏性试验
要突破国际垄断,需要经过不懈的努力。其中,对产品品质的检验尤为重要。
2013年7月,设计额定载荷385 . 5吨的升降单元迎来了又一场考验。在美国船级社验船师和F&G用户的见证下,升降单元测试暴风极限载荷——646吨抬升力。试验结果让人信服,升降单元毫发未损,此后的探伤检测全部正常。
南通传动的升降单元、桩腿、锁紧系统和500吨拉力试验场位于分公司东南角。在这里,每一批锚机、锁紧系统等都经历过严格的出厂试验。
“我们在出厂检测方面的投入是一般小企业无法比拟的,很多产品的测试都能模拟现场工况,确保配套件装到船只上就能投入使用。 ”谈及产品品质,南通传动质量监督部经理王学礼非常自信。
2014年2月18日,美国诺布尔钻井公司亚洲部项目经理丹尼斯在新加坡裕廊船厂工程师的带领下,来到了南通传动。这次用户要求对额定载荷385 . 5吨的升降单元进行破坏性试验。
从生产现场随机抽取的样机装上了试验台。验船师、设计工程师、质检员、 F&G技术人员、公司领导都来到现场,大家的目光注视着屏幕上跳动的示数。
646吨、 816吨、 1000吨、 1200吨、 1335吨……纪录一次次被刷新,升降系统和桩腿的耦合仍然那么有效而稳定。破坏性试验最终也没破坏到升降单元,其后的探伤检测表明,所有零件无一异常。
要想成为真正的海工巨人,就得拥有核心竞争力,解决核心配套件问题。振华重工通过学习、提升、融合、创新,正逐步破解着通向海工强国的密码。从升降系统、重型锚机到铺管船张紧器、动力定位系统等,振华重工正努力开启着海工“中国智造”的新时代。振华重工海工核心配套件的发展之路,带来的不仅仅是丰厚的利润,更多的是启迪和引领。