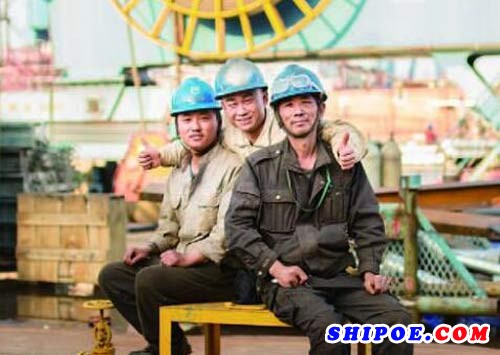
中航鼎衡造船有限公司(简称“中航鼎衡”),由中航国际控股,并由直属企业中航国际船舶发展(中国)有限公司(简称“中航船舶”)受托管理。2017年是中航鼎衡持续抓管理基础、优化生产流程的关键一年,全体干部员工以“打造中小型化学品船建造示范基地”的工作目标为指引,围绕“提质、增效、降本”三大年度工作主题,提质增效工作取得了重要进展。2017年初,船厂通过“SWOT”分析法,结合内外部环境,明确了在安全、质量、成本、研发和效率的“提质增效”具体目标。
安全生产促效益 科技兴安显人本
中航船舶、中航鼎衡将安全生产列为“必须做、立即做、严格做、限时做”且需要“革命性变化”的首要重点工作。船厂相继借助集团公司、总部特邀专家、外部船舶行业专家、第三方船级社、政府安监部门、与中航威海间互查等多形式多次安全检查,通过自查与交叉检查的方式,解决自身可能产生的熟视无睹或长时间见怪不怪造成的隐患,安全隐患整改率100%,“零事故”有效保证了稳定的生产环境,“以安全保效率,以安全促效益”。通过提高技术、运用智能化等手段营造“本质安全”环境,船厂在“科技兴安”方面下功夫,加大资金投入力度,相继引进登轮系统、机舱安全监控系统、APP点检巡查系统等管理软件,借助高科技手段,提升安全监控的及时性、有效性,初次尝到了“高科技”改进粗放式造船安全管理的甜头。以人为本,进一步改善了员工工作环境,努力打造“本质安全”的施工作业环境。
推行“精益”质量管理 稳步提升产品品质
船厂主打产品不锈钢化学品船、双燃料推进动力船等均属高难度、高标准、高附加值的产品,对分段建造、焊接质量、合拢精度有着严苛的标准和要求。为此,船厂将“精益制造管理”作为提质增效的着力点,一方面邀请中航国际商学院开展了“远航—展翅”培训计划;另一方面,针对焊接、合拢成立工艺攻关小组,相继推行无码装配、高效小车自动焊等工艺,加大精度控制管理力度,不断提高中间产品的合格率。
成本攻坚 实现成本管控能力质的提升
船厂开展成本专项管理提升,加强成本管控能力。一是成立成本管理中心,把好成本管控入口,从梳理人工定额、加强审价核减、预舾装托盘定制及整理清理库存积压等多方面着手,促进造船成本有效下降。
二是大力促进采购费用降本工作,通过积极向船东推荐性价比更高的设备、引进合适厂家创造有效竞争局面、减少中间环节等手段,在原材料价格大幅上涨的市场环境下,14艘新船项目的采购成本相较于报价预算,综合降本率硬是达到了13.56%,深度挖掘降本空间。
三是多措施“节流”,降低费用支出,按月对费用执行预算情况进行分析统计及月度考核。
源头入手 流程再造 推进自主设计与生产的有效融合
2017年,船厂依托中航船舶、德他马林(中国)及自身设计力量的有效融合,在16300吨双燃料化学品船项目上开始试行自主生产设计工作,从设计源头入手,优化各类基础资源配置、合理划分分段建造规划、及时沟通优化现场问题,经过首制船的验证,仅货舱区结构优化便减少了用钢量61.6吨,初步达到了预期目标,实现了纸上造船的概念,为后续进一步“降本增效”推进分级、分道制造提供了翔实有力的基础支持。
今年以来,中航船舶和船厂再次针对造船模式转变工作进行了深入研讨,以“提质增效”为导向,从碎片化、单点式向系统化全面推进进行转变,从工位定置、中组建造、总组合拢、高效焊接等多个维度同步走。虽然其间由于经验不足,也产生了成本增加、效率降低的情况,但经过近一年的坚定实施,从生产区域功能划分、计划管理体系、工序优化组合、工艺工法等多方面多维度的优化后,生产流程逐步固化,形成了符合船厂产品定位和资源特点的新流程体系,快速将“阵痛期”落下的工作量逐一完成,船舶建造效率尤其是船坞合拢效率得到了显著提升,进一步提高了核心资源的使用效率。在流程改进后,分段总组率、预舾装率分别从原有的50%、60%提升到现在的80%、85%,其中电气舾装件预装率已达到95%,为缩短船坞合拢周期奠定了良好的基础,同时更为船厂爬坡蓄力、进阶“精益造船”模式奠定了坚实的基石。
建队伍 抓机遇 努力打造船舶制造示范基地
建队伍,夯实核心竞争力。持续优化人力资源结构,建立合理的激励、竞争机制,营造“能者上、庸者下”的用人氛围,并积极借助中航国际商学院资源,开展课程培训,以改变思维方式,打造目标统一、行动统一、价值观一致、知行合一的管理团队。 抓机遇,巩固市场领先地位。随着国际社会对“ECA”、“Tier III”等环保节能要求的日益增高,充分发挥自身在节能型船舶、双燃料动力船舶方面积累的经验,谋求更多的合作机会。同时,坚持差异化市场定位,充分利用“军民融合”中的市场融合,承继航空工业、中航国际几十余年积累的市场优势,利用自身的“全球第一”品牌效应,发挥我们天生基因中的航空探索精神,在中小型化学品船、液化气船等细分领域抓机遇、谋发展,争取更宽广的市场前景。促融合,努力打造示范基地。通过与中航船舶、德他马林的有效融合,践行“互联网+协同制造”,通过工业化与信息化的深度融合,及时收集并分析基础管理数据,探索“精益造船”的管理提升要求,夯实“精益制造”基础,向构建“智能制造”稳步前行,努力朝着打造“国内领先,国际一流”船舶制造示范基地砥砺奋进。