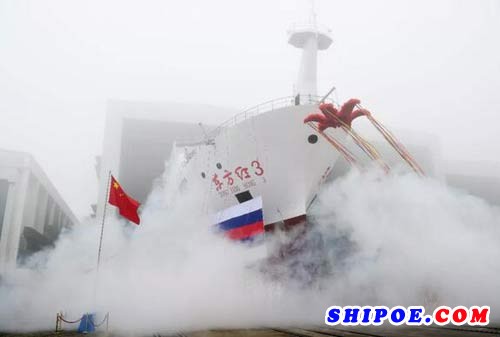
1月18日,江南造船(集团)有限责任公司举行第二届科技创新大会,总结回顾该公司自成立江南研究院以来,在数字化建造、焊接管控、动力系统、舱室环境、噪声治理等方面取得的科技创新成果。
响应市场 重在“落地”
江南研究院成立以来,根据“产品战略升级、科技创新升级、管理流程升级”的“十三五”发展目标,加快核心能力建设,逐步形成了军民技术高度融合的一体化技术体系——研究、开发、设计一体化运行体系,以及以三维体验平台为核心的一体化集成创新平台。
2017年,依托江南研究院的创新成果,江南造船成功交付2艘37500立方米液化乙烯(LEG)船、2艘22000立方米液化石油气(LPG)船、2艘21000立方米LEG船、1艘84000立方米VLGC,同时,还获得了4艘84000立方米VLGC订单,其全系列液化气船的品牌影响力进一步显现。在持续优化VLGC船型的基础上,江南造船又突破了MK-Ⅲ薄膜型围护系统工程化和B型舱围护系统的核心关键技术自主研发,并获得了国际知名船级社的认可。同时,江南造船依托江南研究院核心能力的建设和江南重工制造能力的配套,形成了液化气船液罐设计、制造的能力,实现了自主的液货系统集成配套。
把握方向 重点“攻关”
过去一年,江南造船根据造船业的特点以及船东的需求,花大力气探索科研的切入点,在高效焊推广、减振降噪等领域开展了12项重点攻关。
江南造船在成立江南研究院之初就设立了先进焊接技术实验室,以重点产品和关键技术为方向,攻关液货舱低温钢焊接、超大型集装箱船止裂钢焊接等项目。针对VLGC建造的技术特点,江南造船已在低温钢焊接操作工艺标准、低温钢舾装件的制作安装等方面进行了攻关,通过大量试验,搜集了1000多项宝贵的基础数据,并制定了一套完整的低温钢焊接工艺标准。
协同创新 跨越“孤岛”
目前,江南研究院根据需要重点攻关的技术,已经设立了包括先进焊接实验室、智能制造研究室、振动噪声研究室、基础创新研究室等在内的1个实验室和5个研究室,并将在今年增设舱室环境研究室等2个研究室。
江南研究院采取了聘用教授、项目委托、联合设立研究室(实验室)等多种方式,加强与高校的协同创新。目前,该院已经聘用了上海交通大学13名教授。2017年,江南造船与天津大学、同济大学等高校的创新合作也在不断推进。同时,为了跨越信息“孤岛”,江南造船深入推进信息化重塑工程,全面优化升级设计、生产、管理流程,努力打造信息化建设的独特竞争优势,仅2017年一年,就完成了约100项的二次开发,实船应用也取得了阶段性成果。
智能制造 增进“体验”
应用CATIA V6 软件的好处在于,高度集成了CAD/CAE/CAM等技术,不但构建全三维模型,而且造船的所有专业都在同一个模型里,并支持人因工程学的方法,可以模拟船员在船上的行走、操作运维等,充分反映人在船上的行为,有助于在设计阶段充分发现问题,有效控制更改及造船成本,提高船东满意度。
目前,江南造船已经在“东方红3”号的生产设计方面实现了全三维建模,并且在该船的整船管段制造、13000立方米LPG船的液罐区域管段制造,以及某专项工程的局部船体分段小组立和中组立的工程验证等环节实现了CATIA V6三维交付物的应用。组建了150人的团队围绕数字化转型开展工作,并计划在今年开工建造的大型航标船上实现CATIA V6全流程、全要素的实船应用,力争在2020年全面提升该院数字化研制能力。
这种转变,不可能一步到位,但正是因为坚定地迈出了转变的第一步,江南造船实现从“江南制造”到“江南智造”的创新发展才拥有了希望,具备了不竭的动力。