6月28日上午8时,上海外高桥造船有限公司与往常一样,开始了一天繁忙的生产。根据生产计划,这天将有一艘40万吨超大型矿砂船(VLOC)从2号船坞下水,这也是外高桥造船建造的第五艘40万吨VLOC。
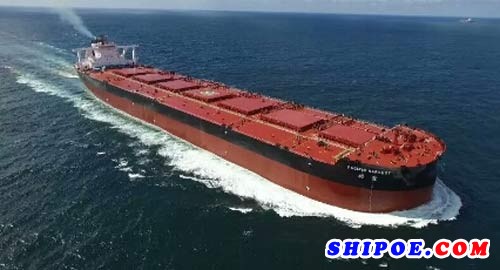
远远望去,这艘VLOC有些与众不同——她不像正在建造之中的“半成品”,而更像是一艘马上要交付的新船。整个船体修饰一新,红蓝相间,特别醒目。甲板上,白色的上层建筑高耸入云,蔚为壮观;机舱里,主机、发动机等设备均已安装到位。
据介绍,该VLOC的出坞完整性达到了87%,而同型首制船的出坞完整性仅61%。这标志着外高桥造船“建模2.0”实现了新突破,朝着世界一流船企迈出了坚实的一步。
从船台到船坞
提升造船完整性
出坞完整性是中国船舶工业集团有限公司实施“建立现代造船模式2.0”(以下简称“建模2.0”)的重要推进方向,也是创建世界一流造船企业、实现高质量发展的标志性工程之一。2015年11月,中船集团正式发布“建模2.0”框架体系,这是我国船舶工业落实国家战略的重要抓手。“建模2.0”的发布,为外高桥造船实施完整性造船指明了方向、增添了信心。
咬住青山不放松,哪怕艰难千万重。在中船集团“建模2.0”框架体系的引领下,外高桥造船以“保持品牌优势,加快高质量发展”为宗旨,围绕“降本与盈利、改善与重塑”管理主题,率先在VLOC出坞完整性项目上实现突破——首制船出坞完整性为61%、第二艘为66%、第三艘为77%、第四艘为82%、第五艘达到87%。
众所周知,船坞、码头是船厂最核心的硬件,而出坞完整性反映了船厂的综合实力。20世纪八九十年代,我国船厂大多为船台造船。由于受到船台承载力的限制,一般新船下水,基本是一个空的船壳,甚至主机等大型设备都要到码头才能吊装。这导致码头舾装周期特别长,严重制约了造船效率的提升。
进入21世纪以来,一批大吨位船坞在各大船企建起来,我国造船业迎来了新的发展时期。船坞造船承载力限制较小,为完整性造船创造了必要硬性条件。
对标“建模2.0”
深入策划生产准备
俗话说,牵一发动全身。出坞完整性涉及方方面面,如管理模式、组织体系、设计理念、物资配套、成本管理、计划管控、工艺工法、信息化、生产准备等,环环相扣,而又形成一个整体,相互制约、相互促进,最终实现“两个一体化”的目标,即“设计、生产、管理一体化”和“壳、舾、涂一体化”。其中,生产准备是重中之重。
围绕“建模2.0”九大核心要素,以及“三翼齐飞”的要求,外高桥造船相继成立了新工艺新工法组、高效生产组、成本管理组、一体化数字化设计组、信息化组5个推进小组,协同推进各项建模工作,夯实各项生产准备。
为了实现高效、连续、低成本建造民船的目标,外高桥造船高效生产组提出了系列中间产品完整性的指标,并构建了各类管理及会议机制,从组织体制和运行机制上提供了支撑。
同时,外高桥造船实施项目制管理,强化全过程协调。由项目经理、商务经理、技术经理、建造经理及质量经理组成的项目组,各司其职,制定、梳理、检查、落实各个生产节点和区域的完整性计划,注重问题解决的及时性、有效性、系统性和连贯性,对出坞完整性负全责。
兵马未动,粮草先行。外高桥造船配套部门以“降本、保供”为主导方针,在开工和船坞阶段,确保物资供应满足船坞完整性之需。
开工前,外高桥造船完成全船钢板订货量的93.17%,整个分段建造阶段钢板配齐率达98.19%;完成116项设备订货工作,出坞前所有物资到货,到货准时率达100%。出坞前,舾装托盘配送完成率达100%。同时,对生产中急需协调解决的问题,外高桥造船相关部门每日进行梳理、逐条落实解决,为完整性出坞保驾护航。
外高桥造船积极推行信息化管理,运用“互联网+”工具,创新质量管理。对标和学习其他行业和企业的质量管控经验,结合自身实际,外高桥造船将过程能力指数(CPK)、故障树分析(FTA)、失效模式与影响分析(FMEA)、六西格玛(6Sigma)等质量工具引入到生产现场的质量管理之中。同时,重点推进质量改善项目:
——管系清洁生产。对管路系统从材料、预制、表面处理、安装、试压、投油、吹扫的全过程建立独立的流转流程。
——EASY-LASER数字化镗孔测量质量改善。在轴系照光过程中应用数字化激光仪直接读取镗孔尺寸,逐步取代传统的光学照光。
——标准化引熄弧板推广。用定制的通用型引熄弧板,取代原有的使用废料和边角料现场切割引熄弧板,全面提升焊接质量。
——利用全新开发的移动端客户端检验APP,在现场及时对检验意见、结果进行跟踪。
——全面推进数字化无损检测系统,在系统内对所有的无损检测数据进行全过程跟踪,从焊接方法、焊接人员、焊接区域、作业时间、缺陷类型等多种因素和角度,对检测结果进行分析。
——针对矿砂船,首次采用了疲劳寿命预测技术。这种技术在售后服务阶段,可持续跟踪船舶关键节点的疲劳寿命,将因船体结构问题导致的事故风险降到最低。
推进坞期优化工程
提高出坞完整性
外高桥造船将坞期优化(出坞完整性)列为企业落实“建模2.0”的重要抓手,旨在以出坞状态作为重点中间产品状态,开展技术创新和船坞计划管控,确保出坞完整性目标达成,进而达到码头周期缩短和可控的目标,提高造船效率。
从2017年5月开始,外高桥造船全面推进坞期优化(出坞完整性)工程。
——建立各生产部门及生产密配部门围绕共同目标协同推进的沟通平台。
——讨论确定出坞完整性的评价指标,包括各区域出坞前的状态,各关键环节、各部门的时间控制节点等。
——确定相似船型出坞完整性逐轮提升的目标。
——各部门围绕出坞完整性目标,进行详细策划。
——相应生产准备工作的配合,包括对内外协物资到货的整体把控,及对场地、设备等资源的协调。
——对号船生产进度的检查与纠偏,包括对船坞建造总体计划的平衡与进度跟踪检查,及对前道分段制作生产情况总体进度把控。
——实时收集整理、分析生产实绩数据,不断优化与完善生产建造工艺标准、搭载网络、中日程计划标准等。
经过一年多的坞期优化(出坞完整性)实践,外高桥造船逐渐摸索出更加合理有效的产品管理路径,成效显着。
强化技术与管理
确保提质增效落地
外高桥造船设计部门持续完善创新以船体为基础、舾装为中心、涂装为核心的设计模式,取得了事半功倍的效果。
精细化设计,提高出坞完整性。不同的施工阶段其施工效率有很大差别。目前常规的舾装作业分为C/B/P/D四个阶段,同一作业在不同阶段的施工工时平均约为1:3:6:9,因此,合理划分舾装阶段有很大的提升空间。
在设计策划阶段,以提高施工效率为抓手,着重对C/B/P/D四个作业阶段进行调整和优化,积极推进基于船体DAP的大组立铁舾件舾装前移计划,采取舾装件预烧覆板工艺,减少反面油漆破坏,以利于脚手架提前拆除。
提高单元化率,提升施工效率。舾装件单元化是提高舾装效率的有效手段。以推进区域综合布置为重点,全面推进全宽型单元、反顶管束单元、功能性单元,以及围绕设备为中心的小型模块化单元,单元设计总数大大提高。
推行完整性建模,提高数据完整性。除极少数软件无法实现的舾装件外,其余小型化舾装件均已实现精细化建模,并提供相关的施工图纸,降低了现场施工的随意性,减少了现场反复测量、调整等工作的时间消耗,舾装件模型完整性程度达到99%。
外高桥造船加强工艺研究,提高工艺水平。工艺设计人员打破原有的框框,主动创新求变,取得成效。
——结构完整性总组工法研究。开展横舱壁结构完整性建造工法研究,通过槽型舱壁与小甲板进行侧态总组,缩短了吊装定位周期,减少高空作业,提高了总组的安全性。
——纵舱壁结构建造工艺研究。采用纵舱壁侧态总组,减少了纵舱壁特殊结构的搭载定位难的工艺瓶颈,提高了纵舱壁结构总段完整性,降低了作业难度,提高了作业安全性。
——船坞并行工程的建造工法。在船坞阶段为实现船坞空间的利用率提升,开展巨型总段位移技术研究,实现VLOC的坞内并行工程的建造工法。
——FCB+SAW高效焊接方法的创新。针对甲板厚板拼板进行焊接工艺创新,采用FCB+SAW的方法,既保留了FCB法高效焊,又使用了16极高速自动焊对纵骨进行角焊。依托流水线自动化程度高和FCB法焊接设备效率高、质量稳定的优势,提升厚板拼板的整体效率。
——垂直气电焊在75度工况焊接工艺的创新应用。传统的散货船建造中垂直气电焊仅应用于90度垂直的舱壁,在VLOC项目建造中工艺研究所通过多次试验,成功实现的75度垂直气电焊的焊接工艺,并通过船级社认证,实现75度舱壁结构的高效焊接。
——船坞快速安装作业平台开发。针对舵叶安装的特点,结合现有作业平台的技术参数研究,自主开发适合能够顶升380吨的舵叶安装作业平台。突破舵叶安装关键工艺装备的瓶颈,确保船坞周期。
为了实现完整性出坞的目标,外高桥造船各生产部门发挥主动性和能动性,相互沟通协调、支持配合。
在平台总组阶段,外高桥造船机装调试部制定了“40万吨矿砂船机舱总段舾装完整性标准”和“40万吨矿砂船出坞机舱完整性标准”,实现总段吊装前百分之百评估,大幅提高了机舱总段舾装完整性。出坞前,机舱管系和电缆敷设全部交验结束,配电板通电,集控台附件安装完整,报警点开通,各项指标都超前达成。
随着工序前移的推进,应急发电机和舵机的调试工作也在船坞内紧张而有序进行,而且仅用3天时间完成应急发电机报验,完成驾驶台整体通电和航行灯信号灯系统的灯桅调试工作,首次实现坞内舵机动车,主发电机和相关辅机设备也达到了可调试报验的状态。
出坞完整性的关键点还在于涂装。外高桥造船涂装部总结同系列矿砂船的建造经验,把关键路径上的两个重点项目——机舱和压载舱作为突破方向。
机舱内环境复杂,交叉施工多,涂装施工对设备安装、调试有很大影响。鉴于这一情况,外高桥造船技术人员把机舱的打磨油漆分解为四个阶段:机舱底层箱柜舱室的打磨油漆、机舱底层、机舱上中下舱室箱柜打磨油漆、机舱整体打磨。施工中,充分利用设备调试安装的间隙,合理安排劳动力进行突击,在完成涂装施工的过程中不耽误其他专业的施工进度,实现了机舱底层11个舱室箱柜在半船起浮前打磨油漆结束,机舱底层起浮后一周完成打磨油漆,出坞前20天机舱舱室油漆完工,出坞前3天机舱油漆整体脚手架以上区域油漆完工。
针对机舱舱室中的重点舱室—淡水舱,为了实现坞内油漆完工,外高桥造船实施了新的工艺流程。淡水舱的常规施工流程顶壁和地板是分两次施工,周期很长,至少需要24天。根据淡水舱油漆的特性以及施工过程中的环境温度(温度高,完全固化时间短),技术人员多次与船东及油漆服务商开会讨论缩短淡水舱施工周期的可能性,最终决定顶壁和地板同时施工 ,减少中间步骤。这一工艺流程的改变,使施工周期由24天缩短到18天,最终实现出坞前5天油漆完工。
涂装的另一个重点项目是压载舱。VLOC的压载舱面积大,舱室高,脚手架多,施工工作量巨大,每个压载舱面积在20000平方米左右,高度有30米左右,想要在短短的58天坞期内完成整体打磨油漆,相当困难。针对压载舱的施工难点,同时根据同系列船的施工经验,外高桥造船涂装部尽量减少搭载后压载舱内脚手架的数量。同时,在分段、总段交涂装之前进行舾装完整性检查,减少舾装件不完整对涂层造成的破坏;工序前移,把后期的高空立体作业分解为平面作业;分段完工拆脚手架后,及时对脚手架损坏的涂层进行修补,并清理会对涂层造成损伤的钢砂、灰尘等污染物,同时做好涂层保护,除合拢缝以外的区域后期不再搭设脚手架。
切实有效的施工手段和方法,使总段的涂装工作量相比原来减少了50%左右,打磨到完工周期控制在5天以内,压载舱整体脚手架数量减少了60%左右,涂装打磨周期缩短2天,压载舱拆脚手架的时间也缩短了2天。
建设一流船企
实现高质量发展
当前,外高桥造船在中船集团“建模2.0”引领下,实现了出坞完整性的新突破,但是离世界造船先进水平还有一定差距,要真正实现出坞全面完整性,任重而道远。而且,完整性出坞是“建模2.0”的一个子目标,目前外高桥造船仅达到87%,在运行系统和管理机制等方面,还有进一步提升的空间,需要补齐短板、精益求精,才能做到极致。
为了实现100%的出坞完整性,外高桥造船将以各个系统的调试为切入点,逐步提高系统调试前的机械完工、管系完工和电气完工。提高坞内脚手架拆除率、舱室涂装率,出坞一周内实现发电机动车,全面达到计划及时性、质量符合性和状态完整性的完工管理目标。
今年5月,中船集团党组书记、董事长雷凡培在外高桥造船调研时指出,要聚焦世界先进水平,对接国家战略,进一步加大机制创新、管理创新、技术创新的力度,以“建模2.0”为抓手,深入两化融合,优化产业结构,努力建设具有全球竞争力的世界一流船舶企业。