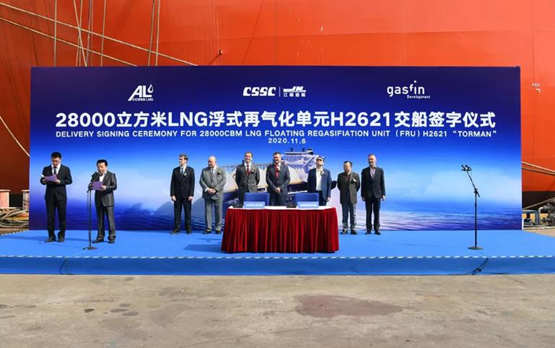
作为海工平台,该平台必须符合海工规范要求。与常规船舶一般以5年为间隔进行入坞检修维护不同,该平台投入使用后25年以内不用进坞,如此长时间的工作,要求该平台必须扛得住磨炼。
全球首制加上质量要求高,为了确保顺利建造,项目组在前期进行深入演练,最终排查识别出此平台建造关键点,包括液货系统、大尺寸液罐、双燃料发电机以及桩柱系泊。为攻克这些关键点,项目团队做出了很大努力。
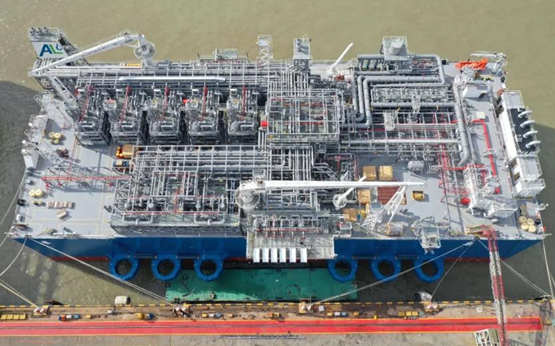
FRU采用IMO C型罐,但与江南以往建造的30000方LNG船的C型液罐不同,它是名副其实的“大尺寸”,其内置罐体长度达74.5米,超出常规罐体长度两倍有余。尺寸的不同导致液罐的驳运、吊装、泵水试验以及液罐建造周期难度都有了较大提升。经过详尽策划,项目组将单罐建造分为22个分段,采用6总段划分建造,确保了建造速度;而为了顺利驳运,公司甚至对驳运涉及的路线进行了重修拓宽。
与常规船舶采用缆绳系泊不同,FRU采用了桩腿式系泊方式——“固定垂直桩加抱箍系泊”。在她的右舷配置了六根江南自主研发的固定抱箍装置,靠岸时候,六根抱箍套入插入海底的六根垂直桩,桩腿的直径粗达2.5米,为了制约水平面上的位移并尽量减少垂直方向的摩擦力。特地在每根抱箍结构内侧放置了四个高分子材料碰垫使抱箍之间留有100mm左右的间隙。保证在系泊海域最恶劣的工况下FRU的定位并承受波浪引起的垂向运动。
文件准备也是“一道大关”,建造过程中不仅需要项目的合格证书,更需要环节中的每一个细节的文本资料。“单单是液货调试的回路检查过程文件,就有6000多页,全部摞起来大概就有近70cm,要小半个人那么高。而这样的检查项在整艘FRU上,数不胜数。
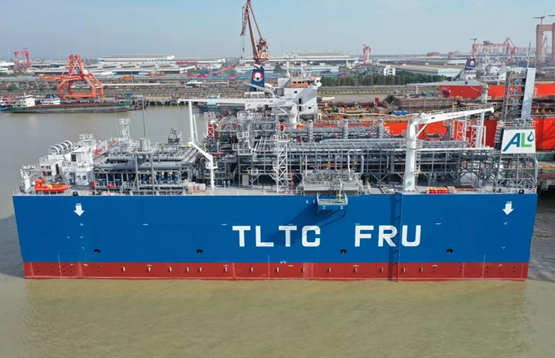
“虽然有首次建造以及疫情影响特别是确保高质量交付的原因,但我们对该项目的进度还是不满意”,平台虽已交付,但建造组没有停止思考,“但有了这次经验,我们相信下一次我们会造的更快”。
据悉,FRU将于明日离厂,踏上前往非洲的征程。