“长荣船东之前长期在日本建造船舶,检验时也习惯采用日韩造船标准进行,而且非常注意细节,这对我们的船舶建造是一种促进和提升。”2500TEU集装箱项目副总建造师杨长弟说。在建造过程中,项目组牵头多个部门,加强与船东沟通,统筹劳动力和生产资源,改变施工习惯,按照节拍化全力以赴拼抢进度,保证了船舶建造稳步推进。
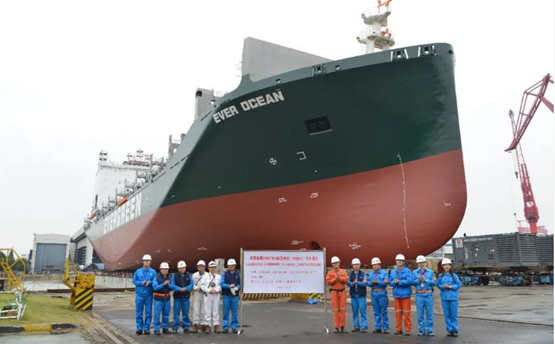
主船体建造过程中,由于0号船台区域吊车资源紧张,且江南造船要求推进总段总舾总涂,搭载一部与搭载二部协同共建,首次在支线箱船上采用异地总段总组,货舱区域两个小环段在异地进行建造;在驳运至船台前,货舱大环缝完成精度测量,对余量进行切割;总段成型后使用模块车驳运到船台,与艉半船无余量搭载合拢,大幅减少了定位时间。
此外,该船的上建整吊工作也是一大亮点。该系列船上建总重达1260多吨,0号船台龙门吊起重能力仅450吨,无法满足整吊需求,项目团队决定租用1600吨浮吊进行整吊作业。为缩短吊装周期、降低租赁成本,项目团队经过数据收集与测量,制定了完整的驳运、吊装方案,保证了上建整吊上船时无余量、无加强,极大地减少了船上作业物量,使浮吊脱钩时间相对系列首制船缩短了50%,有效提高了船台效率。这也江南造船首次尝试并成功实现支线箱船上建无余量搭载,标志着公司精益造船实现重大突破。
在后续的生产过程中,江南造船将继续加强与长荣海运船东建造组的沟通、协作,统筹优势资源,组织好各项码头系泊试验和试航试验,确保按期高质量交付船舶。