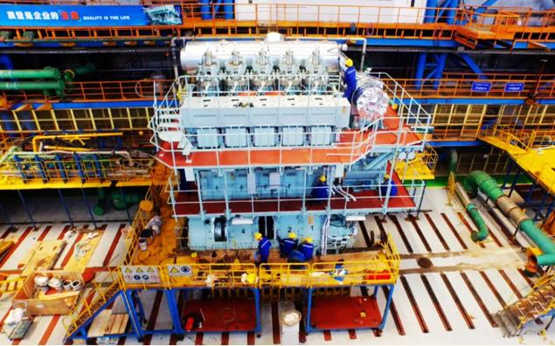
一是根据生产任务、场地功能进行作业区域划分,对辅料、标准件和常用工装工具等物料就近定置,减少人员走动,提高有效劳动时间。
二是设置工位可视化看板,将工位产品质量要求、自检记录、系列机整改和开工交底会议纪要等信息进行现场张贴。
三是以需求为牵引,依据工位计划产生工位物料配送计划、三大件需求计划、行车计划、工装转运计划等需求计划,提前转相关部门以拉动物料和人员的流动。
重点关注首台双燃料主机建造
提前组织对公司首台低压双燃料主机进行攻关,掌握主机建造过程中的重点、难点。有针对性的对厂房、台位进行改造。编制了装配工艺并设计专用工装,提前演练并通过审核。分厂内组织学习交流,在原工艺上多增加试验及测试项目,尽量避免后期出现问题。将安全放在首位,严格按双燃料安全指南要求开展工作,组织员工参加“四新”系列培训。下一步,分厂将具体落实各项要求,重点加强现场问题处理和安全可靠性检查。
巩固PDCA成果
年初,董事长张德林在年度工作报告中提出了降低主机交机后客户整改意见数量的工作目标。总装厂随即组织专题会议并提出多项措施,通过实施过程中不断检查总结,实现了前三季度平均每台机整改意见9.4项,阶段性完成了全年整改意见平均不超过15项的目标。四季度,总装厂继续保持巩固成果,加强系列机在装配阶段物料追踪和整改执行情况,动车前逐项检查,确保系列机整改问题不重复出现;推进交机当天快速反应机制,客户提出的意见当天解决;建立通用整改物料库,做好整改物料的库存储备。