数字化转型、工业互联和人工智能是船舶工业开启智能制造的通关密码。经过多年的摸索积累,中国船舶集团旗下江南造船的智造转型正多点开花。通过数字化焊接、三维弯板机、巨型总段智能对接等关键技术设备领域的突破,追溯一艘船舶制造的全过程,江南造船这一批有点不一样的造船人,用一条焊缝、一块钢板、一个总段,解答着船舶工业智能制造难题。
精确到点见“缝”插针
焊接,将一块块冰冷的钢板连接成有机的整体。江南造船对智能制造的初尝试,就是从一条焊缝开始的。
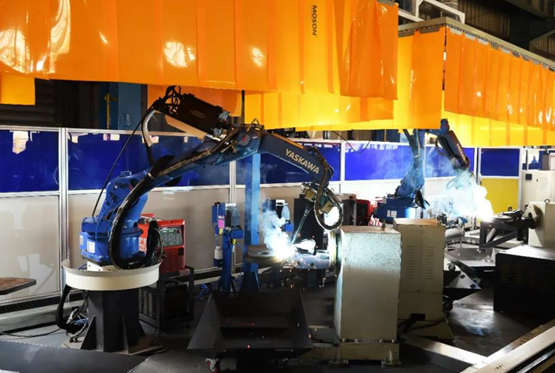
2012年,江南造船联合上海交通大学和多家焊机制造厂商进行专项研发,研制运用了具备联网、预设、管控、评估四大功能的焊接质量数字化管控系统。产、研、用三方各司其职,针对各型钢板的各类焊接需求,船厂设计、制造部门对大量的焊接工艺进行归总、梳理与分类,建立工艺数据库,将焊接规程同焊缝模型关联起来,这些关键数据再交由大学、焊机厂商进行设备的开发与升级。2015年,在一艘液化气船上成功试运行后,江南造船将焊接质量数字化管控系统全面铺开,如今已联通全厂超过1200台焊机。
升级后,焊工仅多了凭证打卡这一个步骤。打卡后,系统会为工人配置工作量和焊接通道;焊接过程中,数字化焊机采用“一点一脉”的工作方式,给每一个工作点都配置最合适的脉冲、输出最精准的电流,同时规范焊工的作业流程,看似生产粗放的船厂也可以实现“毫米/秒级工程”。
江南造船对焊接生产线的智能升级,并没有让机器来取代人,而是让人与机器共舞,在钢板上“苏绣”,使焊接质量从“人控”变为了“机控”。焊接考验工匠的技术、经验,人工作业往往带有一定的随意性;船厂普遍的用工性质,也很容易发生焊工为了提升工作效率而选择调高电流电压参数、加快焊接速度等情况,这些都给焊接质量埋下了隐患。数字化焊接则最大化地规避了人工的随意性,一旦焊接过程中相关参数超过规定区间,系统就会自动报警,再由生产管理人员进行处理。
经过近5年的生产磨合,江南造船的焊接质量数字化管控系统已趋于成熟,现场协调工作也交给了一批年轻、肯干的年轻人,卢斌就是其中一位,他于2017年开始负责数字化焊接相关工作,日常从事数据汇总、任务分派、焊机并联等工作。在现有成熟的系统上,更新工艺数据库、深挖大数据来反向提升焊接有效时间,每天忙碌穿梭于生产车间的这批造船人在提升船厂焊接管控的路上,依旧大有可为。
数字化焊接带来的改变,即便是外行人也能直观感受到。近年来,令众多军迷津津乐道的一点是,我国新造舰船的外壳平顺光滑,难见“瘦马现象”,这就是焊接变形得到有效控制的结果,离不开焊接管控的功劳。
三维弯板不“火”也“形”
做了30年火工的吴一忠,目前任江南造船制造一部加工作业区作业长。从“敲榔头”开始做起的他,如今每天指挥着一台庞大的机器从事着他干了几十年的活——复杂曲面船板成形。
复杂曲面船板成形一直是船厂普遍面临的技术瓶颈,是为数不多的老法师才能搞定的绝活。此前,国内外船厂对单曲板采用冷压、冷弯、辊弯等加工方法,而双曲板加工普遍采用水火弯板的方式。复杂双曲面船板成形一直依赖于工人的经验控制加温和冷却,即便有计算机辅助也很难控制,一直没有实现自动化,是船厂普遍面临的技术瓶颈,而且有经验的“老法师”面临断层。双曲板加工的生产效率和质量都难以提升和保障。同时,一些特种钢不能采用水火弯板工艺,双曲型板加工成难题。
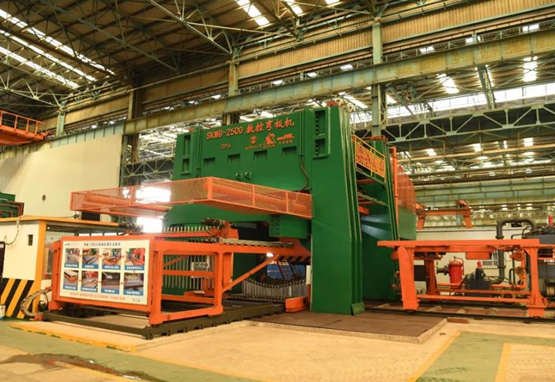
购置三维弯板机后,为了适应设备操作对软件、电气、液压等专业的需要,江南造船招徕了一批专业技术人员,其中包括6名大学生,学数控的王世界、学船机的李亚辉,如今都成长为作业区的得力干将。“这批年轻人对信息化的理解能力、接受能力都很强,操作软件两天就能吃透了。”吴一忠介绍,三维弯板机的操作团队有老师傅、有大学生,大家专业各有所长,在融合的过程中,针对不同钢型、板形的加工方案,做了长时间的积累与总结,在设备的安全性、便利性、可操作性上,团队也进行了诸多改良,“现在这台机器的自动化程度更高了,基本形成了标准,系统可自主决策实现‘一板一策’。”
值得一提的是,相对传统火工严格按规程操作因而一个有经验的师傅通常已不再年轻,使用这台三维弯板机的员工则都是年轻人,他们为机器的使用注入了更多的创新和活力。所以,三维弯板机的使用不只是替代了吴一忠这样的传统火工,而是传统工种在船厂的智能变革中找到了全新的定位和更广阔的舞台。
智能对接“快”“准”得很
从一点一脉、到一条焊缝、再到一块曲面,如今,江南造船的智造步伐拓展到了巨型总段的智能对接。搭载,是将一个个船舶分段拼成一个整体的关键步骤,如果巨型总段在对接的过程中能过做到又快、又准,无疑会大幅缩短建造周期,提升船厂效益。
物体在空间具有六个自由度,即沿X、Y、Z三个直角坐标轴方向的移动自由度和绕这三个坐标轴的转动自由度。巨型总段对接亦是如此,要把两个长、宽、高各几十米的庞然大物,在三维空间进行精准对接,误差控制在1~2毫米,如果按照传统的操作流程,难度大,周期长。
江南造船搭载一部副部长苏宁介绍,传统的巨型总段对接,依靠的多是员工经验,通过计算、靠拢、验证这般循环往复的过程来实现的。首先,船厂会用全站仪来确定巨型总段的三维坐标系,但每一次得出的都是静态数据,巨型总段一旦位移,坐标需要重新测量;对目标移动值的计算,也多靠人工,但总段上各个面的关键点数量大,牵一发而动全身,往往容易顾此失彼;靠拢、位移的过程中,需要油泵小车配合定位,对操作精准度的要求很高;合拢完成后,对接断面的数据也无法测量。
船舶巨型总段智能对接的特点、难点有别于其他行业,该研究于2017年正式启动,上海交通大学、天津大学的科研团队兴趣盎然,集智攻关。天津大学主攻巨型总段的动态定位,通过建立了一个iGPS(indoor GPS)的“毫米”级超大空间三维测量场,利用激光方法,对场内的巨型总段各个端面的测量点进行实时整体测量与运算。上海交通大学主要负责基于测量数据的调姿算法、多车协调控制等技术攻关,将复杂的位移调整数据交给计算机,再由计算机来驱动调姿小车实现毫米级定位,巨型总段智能对接从人为经验判断的较优解到机器智能计算标准解的跨越。
不久前,江南造船的巨型总段智能对接得到了实船应用,苏宁直呼“真香”。以前要爬上爬下看距离,如今在集控室里遥控操作;以前单单用全站仪测坐标要花上几小时,如今巨型总段对接全过程以分钟计……“从我个人而言,真的要特别感谢两所大学,能够解决大尺度、大群组定位真的不容易,这的确是个好东西。”苏宁感叹。
图片