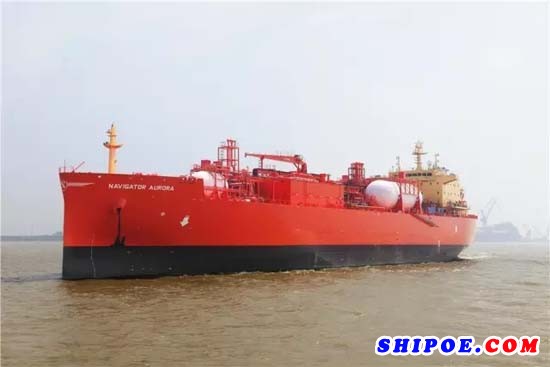
回首“Camel E”首制船的研发、设计、建造历程,江南造船的相关参与人觉得有酸亦有甜。
1能造还是不能造?
英国航海人气体运输公司(Navigator)是江南造船的老朋友。2012年4月,双方签订了5艘2.1万立方米LEG船建造合同。同年11月,该船东又向江南造船提出一个构想,希望建造一型3.8万立方米的乙烯、乙烷运输船,同时,船东对船的主尺度提出了明确的要求——船舶总长不能超过180米。
不超过180米是出于对船舶港口靠泊的考量。总长180米是什么概念?“是1艘中型液化气船(MGC)的尺度,当时全球最长的MGC的长度是183米,而我们这一型船舱容更大,但总长更短。”江南造船研发人员介绍道。2000年,江南造船承建的2.2万立方米LEG船总长170米,2012年签约建造的2.1万立方米LEG船总长160米。如今,船舶总长增加了20米,但舱容提高了60%以上。
首先要确定的,是采用哪种液罐型式。“考虑到乙烷、乙烯快速装卸的需要,那只能是可以承受压力的C型舱。”江南造船产品开发部负责人介绍,在2012年年底,当时已经有非常成熟的3.8万立方米液化气船,但船上使用的是不能承受压力的A型舱。
勾了C型舱这个单一选项,更多的问题衍生出来。C型舱的压力容器通常选择的是承压能力更强的圆柱型、球型封头,如果沿用传统做法,很难实现有限空间下3.75万立方米的总舱容。碟型封头——这是研发团队的第一个想法,这种设计能够大幅节省封头处空间,极大提高船体的舱容利用率。同时,一改之前液化气船4个液货舱的设计方案,该船采用全新的三舱布置设计。
3个C型舱的总体舱容为3.75万立方米,这就意味着单舱装载量要超过1.2万立方米。在此之前,全球单舱容量最大的液化气船就出自江南造船,单舱容积在6000立方米以内,这一次直接要超过世界纪录一倍。这个方案提出后,船东、江南造船内部的一些技术人员都抱持怀疑态度。这么大的液罐,壁板厚度要多大?单罐有多重?这么大的液罐装船后船舶的总体稳性如何?项目研发团队又开始了新一轮的可行性计算分析。
在此之前,江南造船没有开展过液罐的设计工作,为此,研发人员独立自主开发了计算液罐板厚和重量的软件。经过详细的分析计算,液罐外壳的最厚处达到了35毫米左右,比江南造船以往建造的液化气船的液罐厚了十余毫米。
“这么厚的液罐,能造吗?”技术人员详细分析了江南造船曾经建造过的LEG船,虽然其液罐的外壳较薄,但加强环的腹板和面板的厚度也都达到45毫米,既然这个厚度能施工,新船型液罐外壳应该也可以。同时,技术人员在不增加板厚的情况下,提高腹板的高度、面板宽度,以此增强新船型罐体加强环的结构强度。
对当时的可行性论证过程,该项目研发负责人至今仍记忆犹新,在船东提出建造构想的4个月后,江南造船通过前期可行性研究,决定正式开始新船型的研发工作。
2给租家提供方案
在研发初期,没有任何类似的船型技术资料可供参考,技术人员就运用偏差和置信度分析的方法,开展了大量的基础计算和分析工作,结合先进的船体线型CFD计算分析工具,化解了快速性、稳性和总布置之间的各种矛盾和冲突,最终推出了几近完美的总体设计方案。
2013年4月,研发人员着手对船体结构、液货系统和机电系统进行计算分析及验证,保证了船体与液罐的结构具有较强的安全性,液货系统的配置相较于以往的设计更加合理,机电系统的设计采用了最先进、能耗最低的ME-GI双燃料主机。至此,整个船型的技术方案基本成型。
2013年的4~5月,研发人员经常是下班后又陪着在伦敦的船东上班。“船东从租方获得信息反馈给我,我再尽快给他提供解决方案。”产品开发部负责人介绍,就这样,2013年的春天,有8个小时时差的江南造船和Navigator公司人员,为初步方案的敲定频繁进行着邮件沟通,有时一个晚上就是一二十封邮件。经过几轮讨论,2013年5月,租方对江南造船提供的船型方案基本认可,之后又经历了近半年的等待,2013年12月,租方确定货源后不久,江南造船正式与船东Navigator签订了4艘3.75万立方米液化气船的建造合同。
提前介入租家的需求是江南造船的研发思路。随着美国页岩气产业的发展,乙烷作为伴生气也有了不小的运输需求。获取了这样重要的市场信息后,江南造船当即启动了相关船型的研发工作。“不能等船东把什么都定下来了告诉你怎么做,再去研发。那时已经迟了,错过了先机,船东可以选择任何一家船厂建造。”研发人员表示,“在新的市场出现的时候,我们要做的就是根据市场需求、货源需求、货运需求,尽早介入船型研发,在船东尚不知道应该做什么船型的时候,我们给船东和租方提供解决方案。”
3挫折中破土成长
秉持着“用最小的船壳装最大的罐”的设计理念,做好精度控制,将几个“大块头”顺利吊装进舱,成为江南造船建造过程中的重点技术攻关项目。
液罐建造阶段,制造方严控精度,对每个生产步骤作好精度记录并建模,与船舱尺寸进行比对。2015年9月5~7日,江南造船对首制船的2号、3号液罐进行吊装。当时气温在30摄氏度以上,用来固定液罐的环氧材料黏度明显降低,流动性显著提高,加上该船液罐较大,液罐鞍座线型很陡,导致鞍座内环氧在下落过程中发生流挂现象,为此,江南造船设计部同运行部、模块部、品质保证部及液货系统供应商TGE公司人员多次开会讨论,制定了详细的修补方案。
“我们从根本上寻找原因,通过1:1的模拟试验来验证方案的可行性,最终被妥善解决,也为后续姐妹船的建造提供了宝贵的经验。”该船监造相关负责人说。
4成功的密性试验
“Camel E”首制船,还是全球第二艘、国内首艘采用高压主机系统和低压燃气系统的船舶,第一艘船由韩国现代重工承建,交付仅仅比该船早了几个月。
据悉,该船配套了曼(Man)公司的高压主机、瓦锡兰的双燃料发电机组、TGE公司的供气系统。“在前期策划阶段,我们认为各系统之间的硬软件、接口转换会是一大风险点。”江南造船有关负责人介绍说,为此,江南造船召集曼公司、TGE、主机生产商现代重工等各方技术代表一起排查风险、梳理问题、提前策划。“在各方的努力下,我们只用了3周的时间就完成了风险最大的主机燃气调试,密性试验一次完成,非常成功。”
相比之下,双燃料发电机组的调试工作艰难得多,自系泊试验开始至交船,发电机的问题贯穿始终。据了解,由于是新机型首次实船应用,发电机的特性试验、负载试验、燃气调试试验等都遇到了不小的技术难题。调试过程中,双燃料发电机因控制系统问题导致点火油泵损坏,反复拆检更换。同时,围绕发电机的系统,低温淡水、点火油管路、曲柄箱透气、燃气双壁管、燃油循环泵管路都出现了更改,个别管路甚至更改了2次,现场施工难度大,且耽误了调试周期。常规试航前后,船东自己聘请了专家对发电机的性能进行了测试,同时江南造船也相应添置了可以监测三相电压和频率的仪器,大大提高了效率。“为了保障工程进度,所有调试人员和管理人员24小时吃住在船上,不停工。”
5液氮冷罐 迅速又安全
今年7月,“Camel E”首制船开赴扬州进行LNG加注试验。因该型船采用的是双燃料的动力和电力系统,因此需要在甲板燃料罐内进行LNG加注,完成双燃料主机和发电机燃气试验。江南造船此前成功完成了3万立方米LNG船的LNG加注工作,但该型船的燃气系统设计与之完全不同,经过充分的调研和讨论,加注团队决定选择槽车-船的加注方式。
“看到我们对加液方案和应急预案进行了多次演练,供货方对我们这个3万立方米LNG船加注试验的老班底竖起了大拇指。”江南造船有关负责人说。
7月4日,船舶按计划靠泊加注码头,按照既定策划方案有条不紊地进行着加注软管吊装、管路吹扫、密性试验、气体置换、燃气罐预冷、燃气加注、管路放残、加注软管拆除等作业流程。值得一提的是,加注团队这一次开创性地采用了液氮来进行气体置换和燃气罐预冷,同之前普遍采用的LNG相比,液氮的冷罐效率更高,作为惰性气体也更加安全。最终,原计划需要5天的加注试验仅耗时3天7小时就大功告成,为该船后续发电机和主机的燃气试验争取了宝贵的时间。
首制船交付后,江南造船还有3艘“Camel E”半冷半压式3.75万立方米LEG运输船在建。从最初的研发至今,已经历了四轮冬夏,江南造船攻克了研发设计建造的重重困难,首制船锻炼出了一支年轻给力的调试团队,在30岁的调试班长的带领下,2013年后进厂的小字辈挑起了整个燃气系统调试的大梁。就像这支平均年龄不过27岁、由14人组成的核心调试团队一样,技术的不断积累、传承和超越,是江南造船全体员工最大的收获。