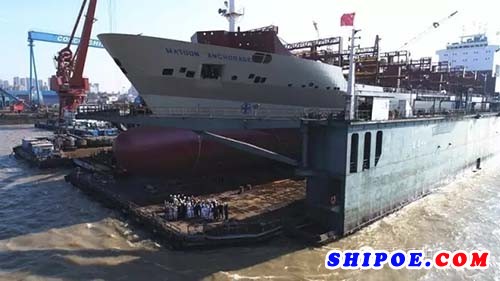
该轮尾柱区域因空间狭小,线性大,且牵涉到整个推进系统今后的工作性能,修理难度极大。之前航次修理时有三次发现裂纹,并在国外其他船厂采取碳刨补焊及局部换新的方式进行过修理,还是避免不了裂纹的产生。此次进厂修理,船方决定采取相邻外板换新并增加板厚和改用高强度材料的方式对整个尾柱裂纹进行挖补,避免该区域裂纹在后续航次中再次产生。
该轮进厂后,修船项目组、船体车间牵头多次召开专项改装策划会,技术方案准备、工装设备等提前做好充分准备。技术部门提前对舵承载荷对坞体的影响进行模拟分析:对整个舵承支撑系统包括舵承静态载荷的承载方法和固定方式,设计和提供支撑液压千斤顶的工装结构和支撑舵承应力的临时工装,编写改装技术方案。由船体车间负责施工准备,确保后续坞内施工顺利进行。
11月3日,该轮进坞后,船体车间主管提前做好各项施工策划。根据设计要求,并考虑舵承的受力情况,液压千斤顶分步加压,最终达到达到总体330吨的载荷要求,从安装开始记录每次加载的变形量。最终加载完成后,比较实际的变形量和预估变形量。舵承下的支撑结构保证支撑牢固不位移后,开始分步拆除改装区域线型外板及尾柱板,然后分步插装艉柱厚板,加装肘板和艉柱肋板。由于外板板厚大,双曲线型加工困难,加厚的新外板与原始外板对接还需加工过渡削斜,同时75毫米厚的尾柱板要求过渡削斜后装配错位不超过±2毫米,材料加工和装配难度可想而知。在第一次预装配不成功的情况下,船体车间攻关小组克服一切困难,连夜找出了解决方案,在凌晨二次装配达到理想的效果。车间精控组提前在外壳在横向中心线上在甲板的横向中心线上,舵承底板的前缘在中心线上,在螺旋桨毂的中心分别设定固定的精度测量点。精度测量为每隔2小时对测量基准进行测量比较分析,确保在误差范围内后方可继续施工。
经过修船项目各部门齐心协力,最终按船方、船检要求成功地完成了所有坞修任务,获得船东的高度认可。该轮也比修理计划提前一天出坞,为该轮按期开航提供了有力保障。